Appearance
Edge Computing: Securing the Silicon Heart of Modern Industrial Automation Systems 🔌💡🔒
Before we delve into the intricate dance of sensors and actuators in modern factories, let's peek under the hood. Because in the world of industrial automation, the chip never lies, and security starts at the transistor. Today, we're navigating a transformative shift in how industrial control systems (ICS) operate, driven by the imperative for speed, resilience, and unyielding security: the rise of Edge Computing.
Why the Edge is Critical for Industrial Automation’s Evolution 🔬
For decades, industrial automation systems have relied on centralized processing, often sending vast amounts of data to the cloud for analysis and decision-making. While powerful, this approach introduces inherent challenges:
- Latency: Critical processes in manufacturing, energy, or logistics demand millisecond-level responses. Sending data to a distant cloud and waiting for a command introduces unacceptable delays.
- Bandwidth Constraints: Imagine a smart factory with thousands of sensors generating petabytes of data daily. Transmitting all this raw data to the cloud is economically unfeasible and network-intensive.
- Security & Privacy: Moving sensitive operational data off-premises increases the attack surface and raises concerns about data sovereignty and compliance.
- Reliability: Dependence on continuous cloud connectivity can lead to operational disruptions if network links fail.
Edge computing directly confronts these challenges by bringing computation, data storage, and network services closer to the data source – right on the factory floor, within the machines themselves, or at local gateways. This isn't just a trend; it's a foundational shift for industrial automation system security and efficiency.
Architecture Breakdown: From Electrons to Insight at the Edge 📈
At its core, edge computing in industrial automation involves deploying compute capabilities at the "edge" of the network. This can manifest in various forms:
- Smart Sensors & Actuators: Devices with embedded microcontrollers capable of local processing and intelligent decision-making.
- Edge Gateways: Dedicated hardware devices that aggregate data from multiple sensors, perform local analytics, and filter data before sending relevant insights upstream.
- Edge Servers/Appliance`s: More powerful compute nodes deployed on-premises, capable of running complex AI models, handling large datasets, and managing localized industrial control systems.
The workflow is simplified yet powerful:
- Data Ingestion: Sensors in the industrial automation system collect raw data (temperature, pressure, vibration, video feeds, etc.).
- Local Processing: This data is immediately processed by edge devices. Machine learning models can detect anomalies, optimize processes, or trigger immediate actions.
- Action & Filtering: Critical actions are taken in real-time, reducing latency. Only aggregated insights or necessary data are sent to the cloud for long-term storage, broader analytics, or strategic decision-making.
This distributed intelligence ensures that crucial operations remain agile and responsive.
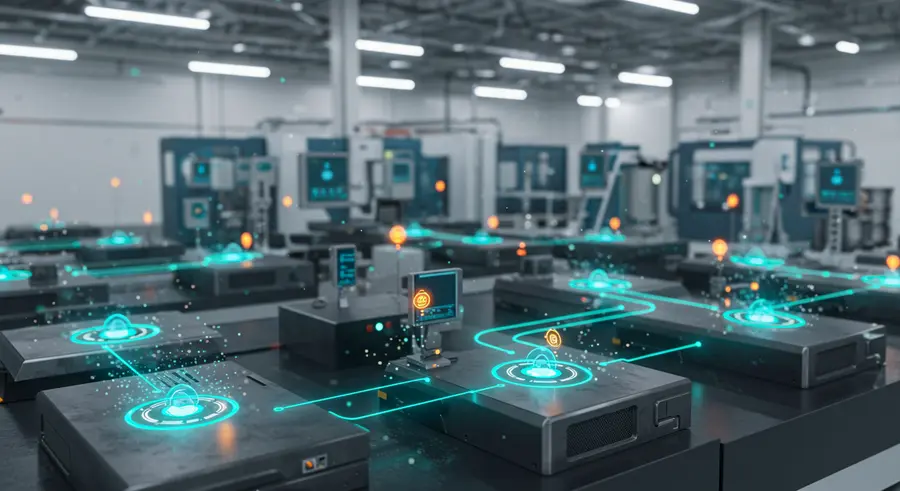
Key Benefits for Robust Industrial Automation Systems 💪
- Real-time Responsiveness & Low Latency: For applications like robotic control, predictive maintenance in high-speed manufacturing, or immediate safety shutdowns, every millisecond counts. Edge computing ensures decisions are made on-site, minimizing delays.
- Enhanced Security & Data Privacy: By processing sensitive operational technology (OT) data locally, the risk of data in transit interception or exposure is significantly reduced. This is crucial for safeguarding intellectual property and complying with stringent regulatory requirements. Secure your silicon!
- Optimized Bandwidth & Cost Savings: Less data needs to be sent to the cloud, reducing bandwidth consumption and associated cloud storage/processing costs. This is particularly beneficial for remote or high-data-volume sites.
- Improved Reliability & Autonomy: Edge devices can continue to operate and perform critical functions even if cloud connectivity is lost, ensuring business continuity in a distributed industrial automation system.
- Scalability & Flexibility: New sensors and applications can be easily integrated into the edge infrastructure without requiring massive overhauls of centralized cloud systems.
Practical Applications & the "Secure by Design" Imperative 🔒
Edge computing is already transforming various facets of industrial automation:
- Predictive Maintenance: Analyzing machine vibrations and temperature data at the edge to predict equipment failure before it happens, minimizing downtime.
- Quality Control: Real-time image processing at the edge to detect defects on production lines, ensuring consistent product quality.
- Autonomous Operations: Empowering AGVs (Automated Guided Vehicles) and collaborative robots (cobots) with local intelligence for navigation and task execution without constant cloud communication.
- SCADA & DCS Optimization: Enhancing the responsiveness and security of Supervisory Control and Data Acquisition (SCADA) and Distributed Control Systems (DCS) by bringing data processing closer to the control elements.
However, with great power comes great responsibility. The distributed nature of edge computing in industrial automation systems also expands the attack surface. This is where Anya's principle of “Secure your silicon” becomes paramount.
Securing the Edge: A Critical Layer of Defense
- Secure Boot & Firmware Integrity: Ensuring that only authenticated and untampered firmware can run on edge devices.
- Hardware-Level Security: Utilizing secure elements (e.g., TPMs) to protect cryptographic keys and sensitive data.
- Access Control & Authentication: Implementing robust identity and access management for devices and users interacting with the edge.
- Network Segmentation: Isolating OT networks from IT networks and segmenting edge devices to contain potential breaches.
- Encryption: Encrypting data at rest and in transit between edge devices and any upstream systems.
- Regular Patching & Updates: A rigorous patching schedule for all edge device software and firmware.
The Horizon: AI, 5G, and Digital Twins at the Edge 🚀
The synergy between edge computing and other emerging technologies promises an even more powerful future for industrial automation systems:
- Edge AI: Deploying sophisticated artificial intelligence and machine learning models directly on edge devices for intelligent decision-making, pattern recognition, and anomaly detection in real-time.
- 5G Connectivity: The ultra-low latency and high bandwidth of 5G will further enhance edge capabilities, enabling massive sensor deployments and more reliable communication for distributed industrial control systems.
- Digital Twins: Creating virtual replicas of physical assets and processes, with real-time data fed from edge devices, allowing for precise simulation, optimization, and predictive analysis.
Concluding Thoughts: The Intelligent, Secure Edge for Industrial Automation 💡🔒
Industrial automation systems are on the cusp of an unprecedented era of intelligence and autonomy, and edge computing is the driving force behind this transformation. By bringing computational power closer to the data source, we're not just reducing latency; we're fundamentally enhancing security, optimizing operations, and building more resilient and responsive industrial environments.
As we continue to integrate more intelligence into our physical world, remember: the chip never lies. Prioritizing "secure by design" principles at every layer of your edge infrastructure is not just a best practice; it's a non-negotiable imperative for the future of truly intelligent and robust industrial automation systems. From electrons to insight, the edge is where the future of industry is being forged.